准确简单地测量磨损量的方法
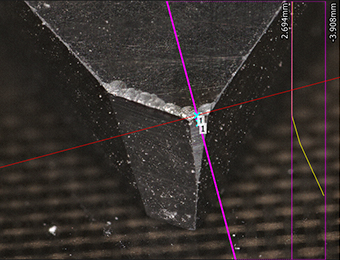
磨损是在工具的刀尖、机械部件的滑动部发生的现象,磨损的量称为磨损量,对这些部件的性能有巨大影响。关于磨损的影响,其引起的发热和振动会造成加工不良,而引起的松动会造成动作不良,严重时甚至会导致设备故障和破损。
会发生磨损的位置必须仔细维护,用油脂等润滑剂来防止磨损。即便如此,磨损仍然是难以避免的潜在危险因素。由此可见,磨损量的测量对于维持产品质量、保𓆉养装置、保障安全⭕来说是必不可少的。
何谓磨损
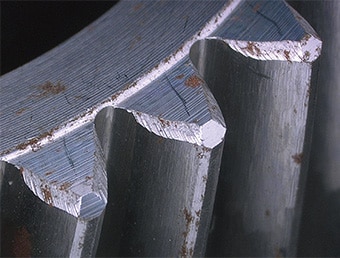
磨损是指摩擦引起的固体表面逐渐减量的现象。也就是说,随着摩擦,固体表面会持续性地减量。摩擦和磨损的现象是外部因素(载荷、速度、温度、环境等)和工程因素(几何学形状、变形、界面状态等)产生复杂性影响的问题。
与磨损相似的现象还有腐蚀(侵蚀),这是流体和固体的摩擦引起的磨损,在配管中的流🤡体和配管之间等处发生。
磨损的种类
磨꧟损是在多种因素组合下发生的,例如作用于摩擦部分的载荷、ꦗ摩擦材料双方的物性、周围环境、热量、温度、物理和化学作用等非常多的参数等,因此磨损的种类有各种分类。此处将介绍其中较具代表性的磨损。
粘着磨损
粘着磨损是指,当2个固体做摩擦运动时,固体表面的突起部分相互接触,结合处(粘着)发生断裂和分离,导致表🍸面磨损的现象。粘着磨损因固体间的化学结合而发生。因此,很容易在以下固体间发生。
- 两个同类型的材料
- 两个晶体结构相同、晶格常数相近的材料
研磨磨损
研磨磨损有多种叫法,如磨削磨损、粉体磨损、粗糙磨损、划痕磨损、♔切削磨损等。这种磨损是在2个固体间,较硬材质的表面突起机械性地削去较软材质,或♐夹在2个固体间的硬质颗粒削去较软固体的现象。其特点是,润滑状态较好,粘着程度少,磨损量多于其它磨损形态。
疲劳磨损
疲劳磨损在相对于轴承的转动面和齿轮的齿面等滑动摩擦,滚动摩擦占主导地位时发生。造𓆉成疲劳磨损的过程如𝔉下所示。
- (1) 反复应力作用于两个金属部件的接触表面。
- (2) 反复应力使表面逐渐硬化。
- (3) 出现细微开裂,发展成龟裂。
- (4) 表面剥离。
产生“(3)”的龟裂的剪切应力在从表面略进入内部的部位处变为൲最大。点蚀和剥落的发生过程同样如上,前者因滚动疲劳而在轴承上造成斑点状微孔(凹痕),而后者在齿轮齿面发𝓀生材料疲劳,从齿面脱落相当大块金属片。
微动磨损
微动磨损是在原本以不发生滑动为前提进行设计的部件接触面间发生的磨损。在通过螺栓或螺母紧固的部件的嵌合部,或者两个部件的接触面上施加反复应力,产生微小的相对滑动(微动),从而发生该磨🧸损。发生微动磨损的面上会出现微小龟裂。此外,外部载荷和反复应力作用于微动磨损部位,因此疲劳强度降至原来的一半以下(微动疲劳),可能导致疲劳破坏。
磨损测量的必要性
磨损直🦂接关系到加工工具的加工质量、部件的动作精度和安全性。因此,测量磨损量和磨损面形状等磨损状态非常重要。作为示例,此处将说明制动衬块和切削工具刀尖的磨损测量的重要性。
制动衬块的磨损测量
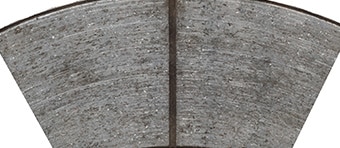
全新的汽车制动衬块厚度约为10 mm。尽管各制造商的产品有所不同,但通常在磨损约1 mm至3 mm时更换。盘式制动器的制动衬块是与制动盘发生摩擦,而鼓式制动器的制动衬块是与制动鼓发生摩擦,从而造成磨损。制动盘和制动鼓也会磨损。制动衬块的磨损面呈现摩擦状态,因此可通过测量或观察其体积和磨损量,掌握制动衬块的耐久性以及刹车时发𓄧生磨损的类型。
刀尖的磨损测量
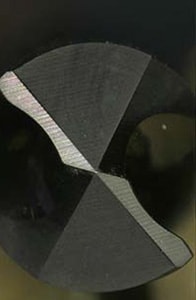
立铣刀和车刀的刀头等刀尖会因为被削物和切屑等摩擦而发生磨损。磨损部位因材质而异,不过多发生于前刀面和后刀面。原因可能是切削速度过快,或刀尖材质不合适等。尤其是难切削的材料,刀尖的负担很大,与加工一般的切削材料相比,磨损量更大。需要注意的是,后刀面的摩擦会造成切削力增大、切入量发生变化。
由此可见,测量刀尖磨损在评估切削速度和刀尖材质选择方面非常重要。
磨损量测量课题
在此之前,人们💝用形状轮廓测量仪和三坐标测量仪测量磨损量🎀。但是,在测量大面积磨损面和微小部件的磨损量时,会存在以下课题。
利用形状轮廓测量仪测量磨损量的课题
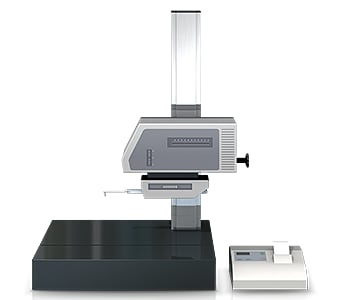
形状轮廓测量仪是使用被称为探针的触针,沿目标物表面移动,对其轮廓形状进行测量、记录的装置。近年来还出现了用激光代替触针,通过非接触式的轮廓描绘,实现复杂形状测量的机型。部分机型还能进行上下两面的测量。
对于想要测量的磨损量和磨损面形状,形状轮廓测量仪必须准确描画测量线。
因此存在以下课题。
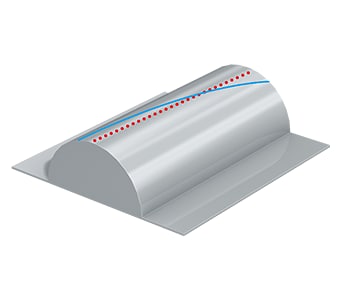
- 将样品固定于夹具、对样品实施水平调整等作业十分耗时。而且,为了准确地实施水平调整,必须具备形状轮廓测量仪的相关知识和技能。
- 形状轮廓测量仪的触针以触针臂上的支点为中心上下进行圆弧运动,而触针前端位置也会沿着X方向移动,因此X轴数据会发生误差。
- 使针按照预期通过的作业非常困难,针的微小偏移就会造成测量值偏差。
- 因为必须对准特定位置实施测量,所以很难增加测量数。
- 由于只能取得部分测量值,无法以面为单位进行评估。
三坐标测量仪的测量课题
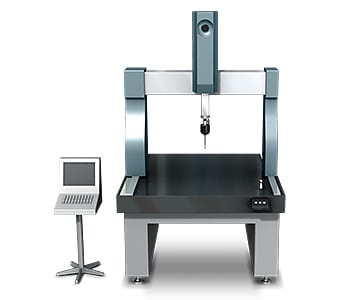
例如,当磨损部分面积很小,只有1 mm2时ꦚ𒊎,要用探头对准该位置,制作虚拟面并准确测量,是极为困难的。此外,测量微小部分的三维形状时,测量点更少,难以准确掌握形状。而且,统计测量数据、与图纸进行比较等工作需要花费大量精力。
磨损量测量的课题解决方法
接触式测量仪对于立体的目标物和测量位置,总是在以点或线接触的同时进行测量。因此存在难以掌握整体形状、测量值可靠性低等课题。为解决这些测量课题,K8凯发开发了3D轮廓测量仪“VR系列”。
以非接触的方式,以面为单位来准确捕捉目标物的3D形状。此外,最快1秒完成载物台上目标物的3D扫描,高精度地测量三维形状。因此,测量结果不会产生偏差,可瞬间实施定量测量。下面具体介绍൩这些优点。
优点1:最快1秒内只需一键即可收集80万点的点群数据
以“面”为单位测量大范围形状,并收集80万点的点群数据。不是利用线或点实施测量,因此无需重新测量。可缩短测量时间。磨损量等难以定义的项目,也可通过体积和表面积来评估,还能轻松地定量评估平面度。此外,可测量各个位置的轮廓。测量后不必再次安装目标物,可从3D扫描后的数据获取其它位置的轮廓数据。
而且还可保存各个测量数据,比较已保存的各数据,或与3D设计数据进行比较。
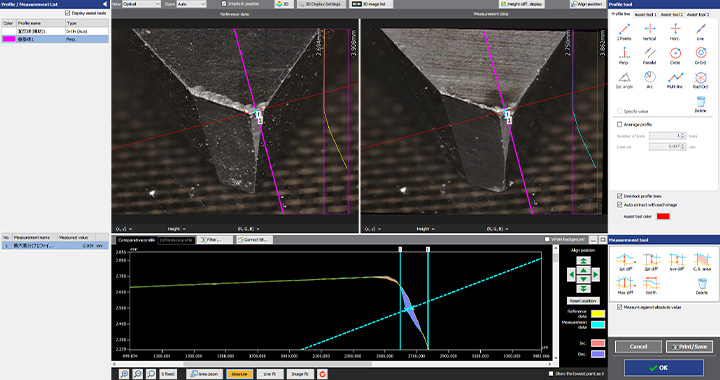
优点2:可测量最大300mm×150mm的大范围
测量所需的作业是,将目标物放置到载物台上,然后只需按下按钮即可。无需严格定位等预先准备,即使没有测量꧑仪的知识和经验,也能立即实施高精度测量。
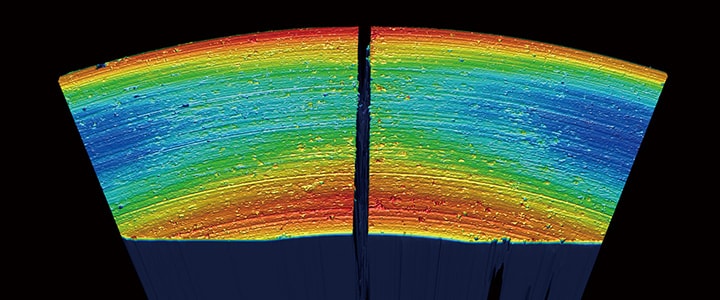
可提取载物台上放置的目标物的特点,自动补正位置,因此省去了耗时耗力的、严格的位置调整工作。此外,还可将达到300mm×150mm的大范围进行拼接测量。因此,测量作业无需配置专人操作,不熟悉操作的人员也可轻松快速地完成测量。
采用“VR系列”,通过只需放置于载物台并按下按钮的操作,即使是大型制动衬块等大面积目标物,也🌸能准确测量磨损量。
总结:对困难的磨损量测量进行飞跃性改善和高效化
采用🐟“VR系列”,可通过高速3D扫描,以非接触的方式迅速、准确地测量目标物的3D形状。除磨损面的最高点和最低点以外,在体积、截面面积、表面积与截面面积的比例等测量中,也可解决接触式测量仪存在的各类课题。
- 周密、高精度地同时测量最高点、最低点、面积、体积、表面积。
- 消除了人为导致的测量值偏差,实现定量测量。
- 无需定位等操作,实现只需在载物台上放置目标物后按下按钮的简单操作。避免了配置专人执行测量作业。
- 简单、快速、高精度地测量3D形状,因此可在短时间内测量多个目标物,有助于提升质量。
另外,还能进行简单分🤪析,例如与以往3D形状数据和CAD数据的比较、公差范围内的分布等,因此可😼有效应用于产品开发和制造的趋势分析、抽取检测等各种用途。